News & Insights
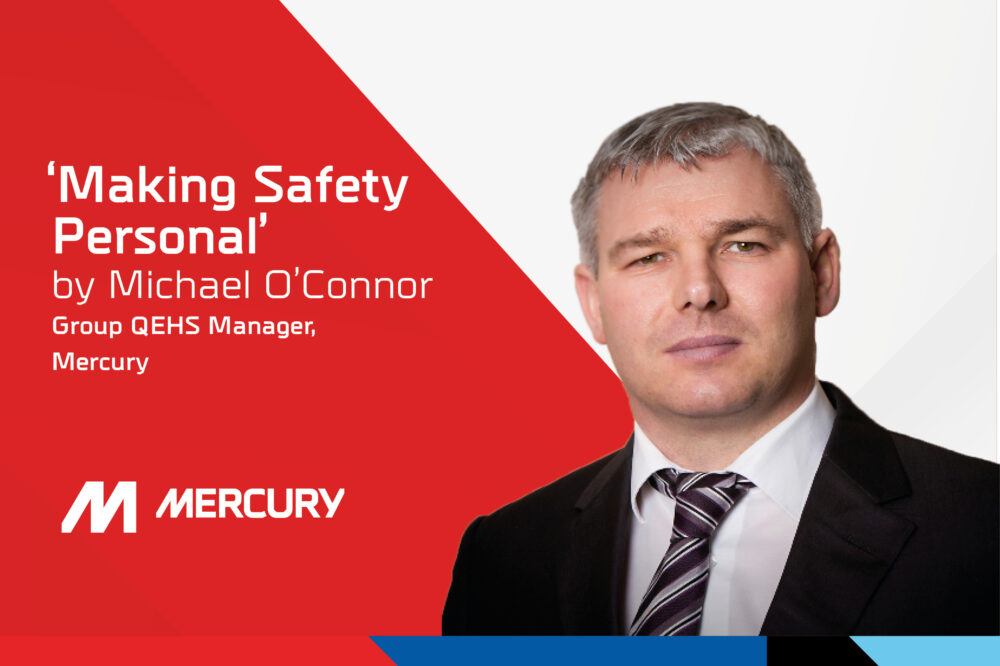
Insights: Making Safety Personal to prevent on site accidents – a success story
Making safety personal through the use of behavioural psychology programmes is key to reducing on-site accidents, writes Michael O’Connor.
Mercury’s health & safety culture is recognised across Europe as industry leading. From our senior management to our trades and apprentices, safety is embedded in our DNA and our daily work practices. In fact, many of Mercury’s safety initiatives have been implemented globally across the construction industry.
When your safety systems and performance are recognised across the industry and by external auditors as world-class, as a company you have a choice whether to become complacent or decide to follow a continuous improvement journey. This ‘journey of inches’ has best been described in the famous speech in Any Given Sunday, made by an American Football league coach played by Al Pacino.
“The inches we need are everywhere around us. They’re in every break of the game, every minute, every second.” – Tony D’Amato, Any Given Sunday (1999)
In order to ensure our safety culture continues to modernise and innovate, Mercury have implemented Making Safety Personal (MSP) training, making a journey of meaningful measurable improvements to EHS performance.
What is MSP?
Making Safety Personal (MSP) is our trademarked behavioural safety and wellness programme. Ultimately, it is a training class with a difference in that it is extremely personal, examining each individual’s relationship with safety and aiming to improve it by reiterating why we work to live and considering how all the people and activities that one enjoys outside of work would be affected by personally taking a chance and not following the plan, causing injury.
The training class is supplemented by a monthly campaign that ensures the key focus topics of the class are not forgotten and are consistently communicated and monitored and measured to ensure improvement. The feedback highlights where immediate improvements can be made and on a monthly basis this ongoing honest open feedback adds immediate and long-term value to the team and client.
When participants have been asked whether the course has affected their personal relationship with safety, 100% of attendees so far have answered in the affirmative. The training has helped to embed safety and wellness in our teams’ DNA instead of simply in their short-term memory.
Results
On multiple Mercury project across Ireland, the Netherlands, Germany, Denmark, Sweden and the UK, our project management personnel are being trained in MSP before any other staff to set the cultural expectations and to bond the teams by building relationships in an open and honest forum where people became more than simply colleagues, developing a more personal relationship together.
With over 50 projects without an Lost Time Injury (LTI) thus far in 2019, Mercury’s safety compliance and cultural journey is a resounding success. It is very important to note that MSP does not take the place of existing EHS systems and the hard work of our committed management and EHS personnel, it is rather an addition to aid measurable continuous improvement.
New Perspectives on Safety
The main two perspectives discussed within the safety community are Safety-I (the historical approach) and Safety-II (looking at safety differently). The two perspectives have been presented in some quarters as mutually exclusive. Mercury have always embraced Safety-I but have always also allowed for open and honest feedback aligned with two-way communication and a reliance on competent personnel speaking up and providing their inputs at the right time.
“Silence is your enemy” is a key message delivered as part of MSP. So is personal accountability for both management and our installation specialists. The embedding of high-risk activities (HRAs) identification and analysis as part of The Mercury Way ensures we are not reliant only on Bird’s Triangle, developed 50 years ago, as a means to proactively prevent incidents. These two concepts are managed together as our experience and performance prove it is a methodology that works successfully.
The initiative is known as High Risk Unwanted Conditions (HRUCs) and is included in the MSP training and Mercury’s Group-wide inductions. Deviations from the plan and personnel working (always non-maliciously) beyond their scope of expertise are two of the three HRUCs. Mercury recognised the issue with behaviours for both those planning and putting people to work aligned with the behaviours of those completing the work.
The HRUC programme changed our auditing focus across the group, (audit for deviations from the plan – intervene / fix / trend and improve) to the point where one of the key messages that we have developed is – if our teams stick to the plan, we will always guarantee their safety. That is a major commitment to our teams which includes all sub-contractors across all the sectors and regions where we work across Europe.
In an industry that occasionally can become jaded with short-term fixes to realign people, it is reasonable to state that all of us through no fault of our own, have scientifically proven inbuilt risk taking as a daily option as part of our normal cognitive process, particularly when under time pressure. As Daniel Kahneman has written in his study on behavioural psychology, Thinking, Fast and Slow, cognitive psychologists have discovered in recent decades that switching from one task to another is effortful, especially when under time pressure. People will sometimes do what is easier for them in the moment rather than thinking of all the consequences.
This undeniable scientific fact alerted Mercury to the need for something different, a programme to attempt to eliminate chosen deviations from the known safe plan, chosen deviations despite a clear message from Group leadership that Mercury does not want anyone to take chances with their personal safety on our behalf.
Making Things More Personal
The MSP training includes a wellness module which gives attendees even more reason to work to live as they consider the effects of taking one chance and the effect to them, their colleagues and most importantly their loved ones at home. A conversation is completed with their nearest and dearest. This is one of the factors that makes this training the most personal of its kind on a global level – and when it is personal, it is effective.
The training which includes multiple cognitive tools to refocus our teams is slightly left field and it is for this reason that it is memorable and interactive. MSP is not the same as other training, the definition of insanity is doing the same thing over and over and expecting different results. Making things personal makes things different, and the key messages of the training are continually communicated at toolbox talks and focused groups to ensure the messages nor the impact never stops. The feedback has been incredible, and MSP is now a key part of The Mercury Way. It has improved our sub-contractors’ EHS performance in multiple countries with personnel of multiple nationalities and languages with no difference in the effects or feedback provided.
Health & Safety at Mercury
We are dedicated to achieving the highest possible standards of Health & Safety. Safety is embedded in our DNA, it is the Mercury way – from design to construction, commissioning and handover – our safety processes ensure adequate coordination and communication to enable our projects to be constructed safely. Our team understand that by sticking to the safe coordinated plan we can guarantee that our team get home safely to their families at the end of every day.
Safety is personal and our team intervene proactively to ensure compliance day by day and hour by hour. We respect our workforce and they respect our management as an integrated team with a common goal – to get home safe each day. Through our Environmental, Health & Safety (EHS) policies and procedures, we ensure an industry leading project delivery every time and most importantly – the safety and wellbeing of all our employees.