News & Insights
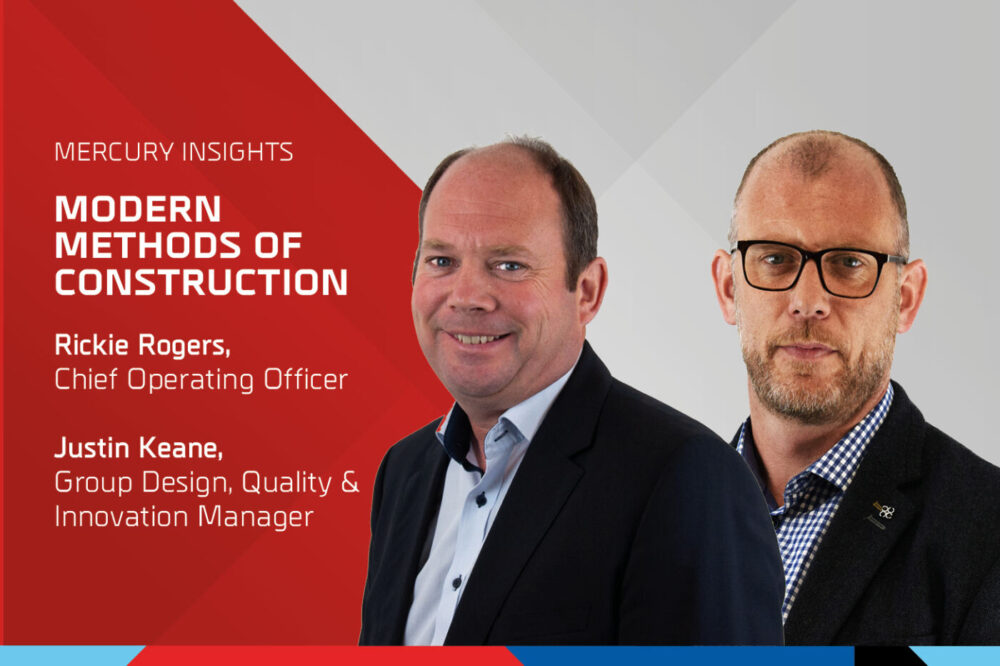
Insights: Modern Methods of Construction
Mercury’s COO Rickie Rogers and Group Design, Innovation & Quality Manager Justin Keane were recently interviewed in Irish Building Magazine, in part of a series on Modern Methods of Construction (MMCs). MMCs is a broad-term, embracing a range of offsite manufacturing and site-based methods that provide alternatives to traditional building methods.
Modern Methods of Construction
Mercury Engineering is a great example of a leading contractor delivering a broad offsite offering across many sectors and countries. Mercury’s work indicates what methods leading contractors will be expected to deliver in the near future.
Mercury operates its own offsite manufacturing facility to cater for high purity and hygienic piping systems which strategically located in Newbridge, County Kildare, with motorways linking it to the head office in Sandyford, Dublin, the company’s Digital Hub in Maynooth and most importantly within 45 minutes of Dublin Port extending Mercury’s reach to Europe and beyond.
Mercury’s Rickie Rogers, Chief Operating Officer and Justin Keane, Group Design, Innovation & Quality Manager tell us they are utilising MMCs and offsite manufacturing (OSM) in various ways across all Mercury’s business sectors: hyperscale and enterprise data centres, building services, life sciences and advanced technology, healthcare, fire protection, and technical support services.
They are seeing positive returns and delivering benefits to clients. “As a contractor with whole lifecycle scope, delivering design, build, commission and operation Mercury are constantly evaluating innovative ways to improve our delivery. Offsite manufacturing combined with leveraging the use of virtual model data has a positive impact on all major pillars of construction: safety, cost certainty, programme and quality, offering significant benefits in all four areas that simply cannot be ignored.”
Facilitating the use of these advanced technologies also encourages sustainability with less waste in the construction sector. They say the contractor is learning continuously about innovations from working in a range of countries. “As our geographical reach spreads from Ireland and the UK to continental Europe, the Nordics and beyond, we too learn from these regions increasing our rate of innovation within this critical and prosperous space.”
As Mercury’s business is diverse so too is the range of offsite manufacturing from fully completed chilled water pipework systems to fully coordinated MEP risers and above ceiling sectional horizontal services distribution to high-purity cleanroom grade systems. The Mercury team are innovators in delivery, going beyond the norm to deliver to site, showing what is possible. “While projects usually drive modular construction to a single load i.e. the size of a 40ft container, we often brake that mould, recently manufacturing an OSM piece of 84inch process pipework, 30m in length, 10.5m wide at a weight of 85 tonnes utilising a 16 axel Self Propelled Modular Transporter to transport this element to the site, on difficult terrane!”
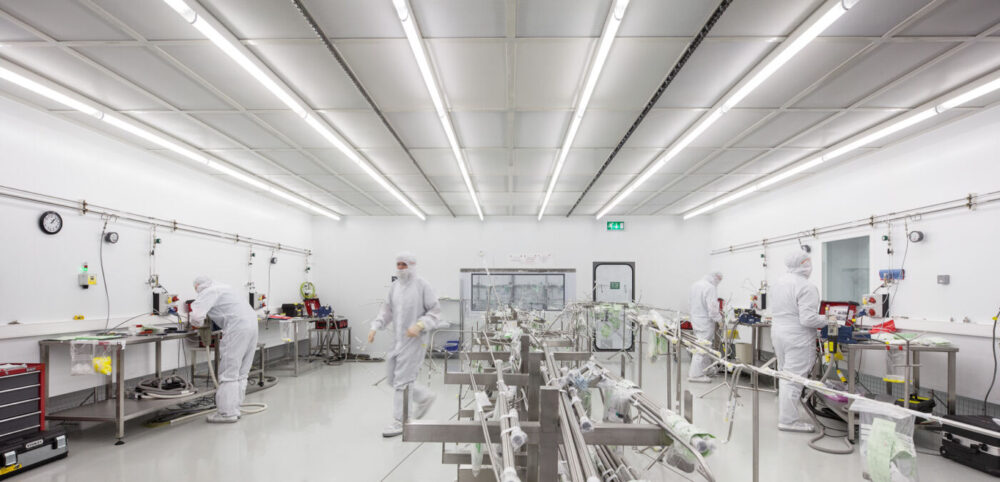
As some of Mercury’s business units have a higher degree of repeat work than others, this, fortunately, lends itself to the OSM processes and procedures they tell us. “As the type and scale of offsite manufacturing varies, so does the value on OSM across the business comprising anywhere from 5% to 35% of the overall contract value and we see this in positive growth.” Mercury’s team feel they hold a distinct market advantage in offsite manufacturing, having evolved from a tier 1 MEP subcontractor to a prime contractor with over 80% of work being direct to clients.
Rickie and Justin say the value-adds for clients come in many forms through the use of the OSM process. “Risk is significantly reduced as work is carried out in a much more controlled environment than that of a building site. Offsite manufacturing supports our ‘Work Safe, Home Safe’ value along with our promise to always deliver.
The process is much more efficient than carrying out the works out on site, as staff are more comfortable in temperature-controlled areas and as a LEAN process that is timely, efficient, and defect-free. Data is recorded on an ongoing basis and in real-time facilitating Mercury’s continuous quality improvement cycle and supporting more accurate cost estimation. Our offsite manufacturing facility is certified to a cleanroom Class 10 standard facility.
This enables Mercury to manufacture, package, and deliver the product to the site without cross-contamination and in a sustainable fashion supporting mainly life sciences and advanced technology.” As Mercury’s digital strategy develops, its land borders are diminishing. “We have refined these processes and fully digitalized them to such an extent that we can confidently move them to any country in the world. As often with these disruptive technologies and processes, it can be more difficult to get the process working efficiently than get the actual product produced”.
Through R&D Mercury continuously evaluates the trade-offs between offsite and onsite manufacturing. Going forward Mercury will continue to research, examine, and improve upon management and installation methods for offsite manufacturing. “We are currently looking at technologies that utilise 4D modelling to reduce non-value-add activities, facilitating greater insights into the visualisation of the complete module manufacturing process considering safety, material selection, equipment, workflow, and people.”
Read the full article here at Irish Building Magazine.