News & Insights
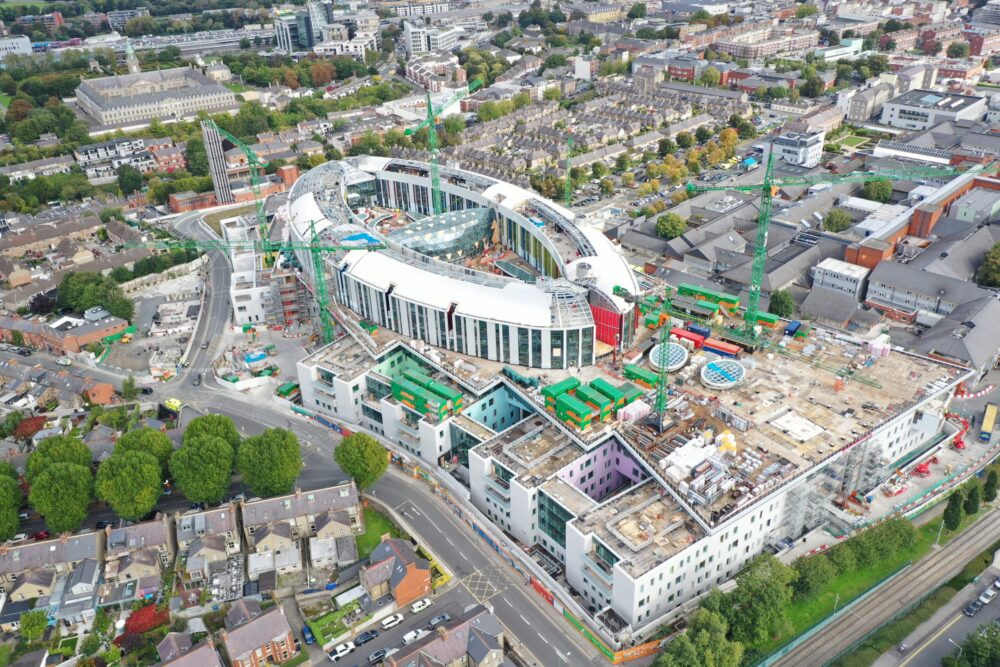
The New Children’s Hospital: Delivering a ground-breaking project with a Digital Edge
Mercury continues to deliver electrical works on the construction of the New Children’s Hospital (NCH) in Dublin, Ireland. Throughout the course of this ground-breaking project, we have utilised a range of cutting-edge, digital technologies, which have enabled our team to deliver major milestones with certainty.
Progress has been significantly aided by the adoption of efficient digital tools, including 3D Laser Scanners, Robotic Total Stations, 360° Photo Documentation, 4D BIM Modelling, and Construction Management Software.
The NCH project is the most significant single capital investment project in the history of the Irish healthcare system. It will bring together the services currently provided at three Dublin children’s hospitals into a state-of-the-art, custom-designed, digital-first facility, that will deliver the best care and treatments for Ireland’s sickest children and young people.
At Mercury, we think beyond the conventional and forge new paths to innovate and operate at the leading edge of our industry. Our solutions help deliver technologies that connect people, communities, and businesses, giving them the power to achieve incredible things.
Read below to learn about the digital technologies Mercury is leveraging on this project.
3D Laser Scanners
Our team are digitally recording the installation of all electrical services before client handover on this project. Traditional methods of documenting ‘as-built’ drawings and models are simply not accurate enough for integration into our BIM Model.
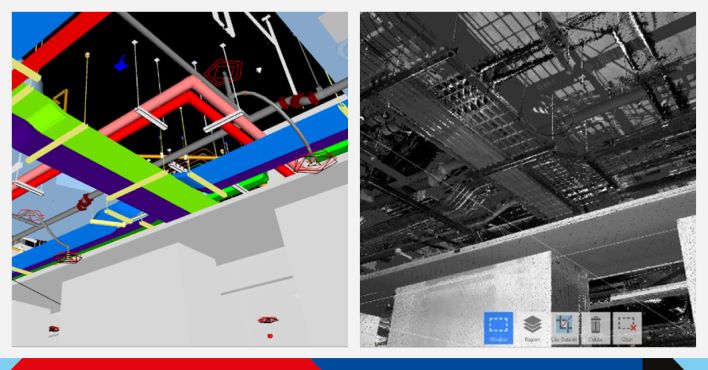
As a result, we are using Trimble’s X7 3D scanner to increase accuracy and efficiency, while addressing this challenge. The 3D scanner allows the project team to scan all electrical services within 6,500+ rooms, with millimetre accuracy.
These scans are imported into the 3D BIM model through Navisworks, meaning that we can verify actual installation on site, against the planned model. Our team can then adjust the model to record the actual real-life installation. This solution ensures ’as-built’ drawings and models are accurate, and our dedicated BIM department can identify any deviations from planned install location against the actual install.
Robotic Total Station
The Trimble Robotic Station (RTS) utilises a high-powered laser to visually mark points throughout the project from the 3D BIM Model. This tool allows set-out services to be carried out five times faster than traditional methods, while ensuring the highest levels of accuracy.

The RTS provides pinpoint laser measurement, to a tolerance of 1.5mm over distances as great as 100 metres. This implementation of this tool contributes to reduced overheads, and ultimately leaner project delivery.
You can learn more about Mercury’s use of the RTS here.
360° Photo Documentation – Open Space
The implementation of 360° cameras is invaluable to our planning team on this project. Placed on top of a mounted hardhat, users can visually capture their full surroundings in one swoop. These images, known as ‘photospheres’, can display the same range of information as up to eleven traditional photographs.
Using 360° photo documentation software, these visuals are automatically stitched and mapped to the project floor plan, creating a 3D digital image that can be navigated by project management.
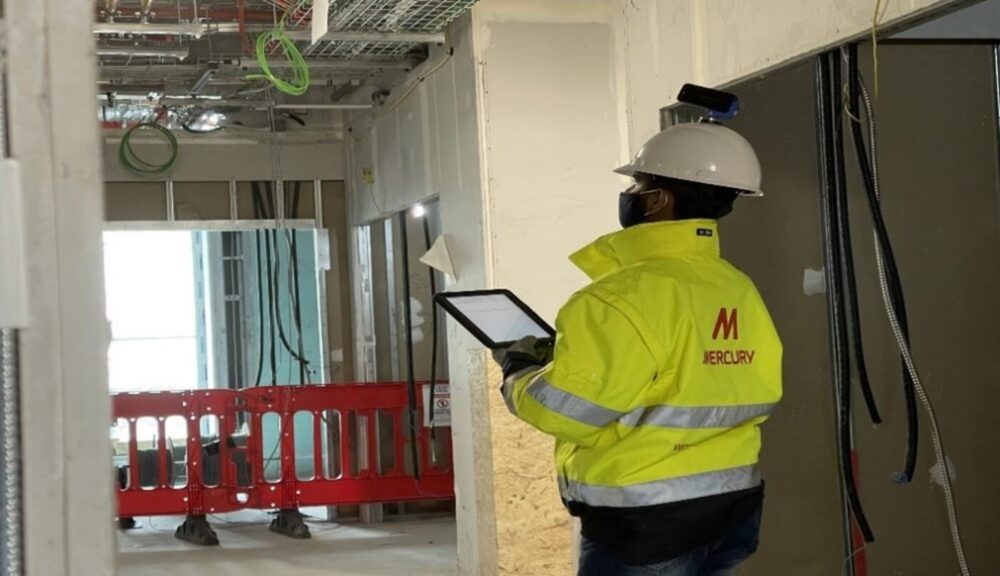
This allows the team to capture the status of the project at different points in time, and these walkthroughs can be used for conducting weekly site meetings more efficiently. In addition, the technology can be used to highlight and amend potential snags.
Barry Boylan, Planning Manager said: “OpenSpace has allowed the entire team to visualise the actual status of the project at different points in time. The historical record that OpenSpace creates is invaluable in terms of dispute resolution, for example, proving the status of an area on a planned start date. Previously this kind of information was available in the form of pictures and videos stored on phones and transferred to shared folders which is time-consuming to manage. Seamless 360 photo walkthroughs through OpenSpace have been a worthy addition to our digital tool box.”
For more information about our use of 360° Photo Documentation, please click here.
4D BIM Modelling – Synchro
4D BIM Modelling allows us to integrate the project schedule with the on-going construction model in real time, as it happens. The construction model captures more detail as the project progresses. This information is stored in the cloud, where it can be exported to various other applications such as Power BI, site tracking apps, and Microsoft’s HoloLens.
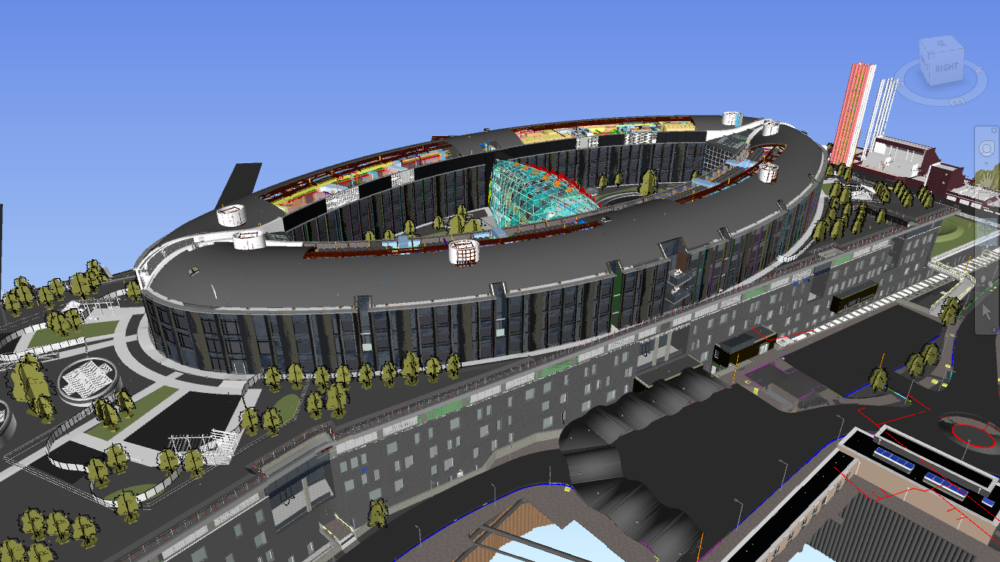
4D scheduling removes a lot of uncertainty before and during the pre-construction stage of projects. We can anticipate issues in advance, optimise project plans virtually, and can eliminate sequencing issues before commencing works.
Barry Boylan added: “By linking the 3D model to the programme, we have created a visual representation of the construction sequence, leading to better collaboration and engagement with project stakeholders. This 4D model is also used to track progress and plan works ahead more accurately, ensuring we stay committed to the project timeline.”
Learn more about Mercury’s use of 4D BIM modelling here.
Construction Management Software – Autodesk BIM360 Field
Document control plays a crucial role in the delivery of complex projects such as data centres, semi-conductor plants, and large-scale health care facilities.
We have standardised and implemented our quality documentation control approach through Autodesk BIM360 Field. This has empowered us to fully digitalise quality processes on site, providing transparent reporting metrics, and reducing overall risk.
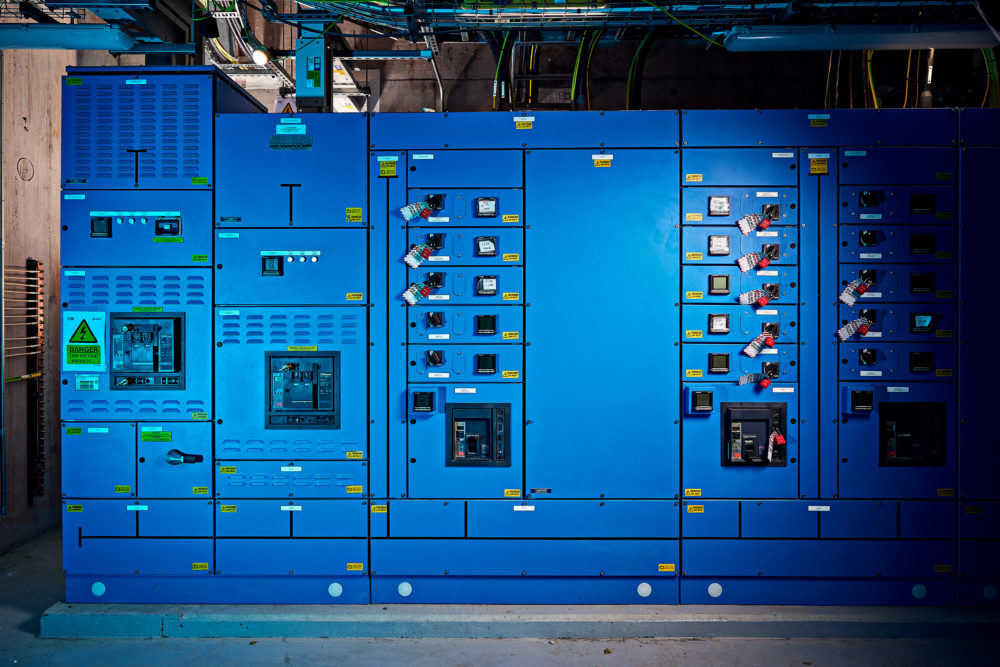
Our system leverages integrated QR codes, allowing users to digitally move throughout the project seamlessly. With the use of a tablet, our quality teams can control all mechanical and electrical assets, and review progress of rooms, while checking snags, checklists, benchmarks, NCRs, and quality audits.
This has truly transformed day to day operations on site, and our teams now have more control over quality. Ultimately this contributes to better risk management, as well as increased organisation, and visibility.
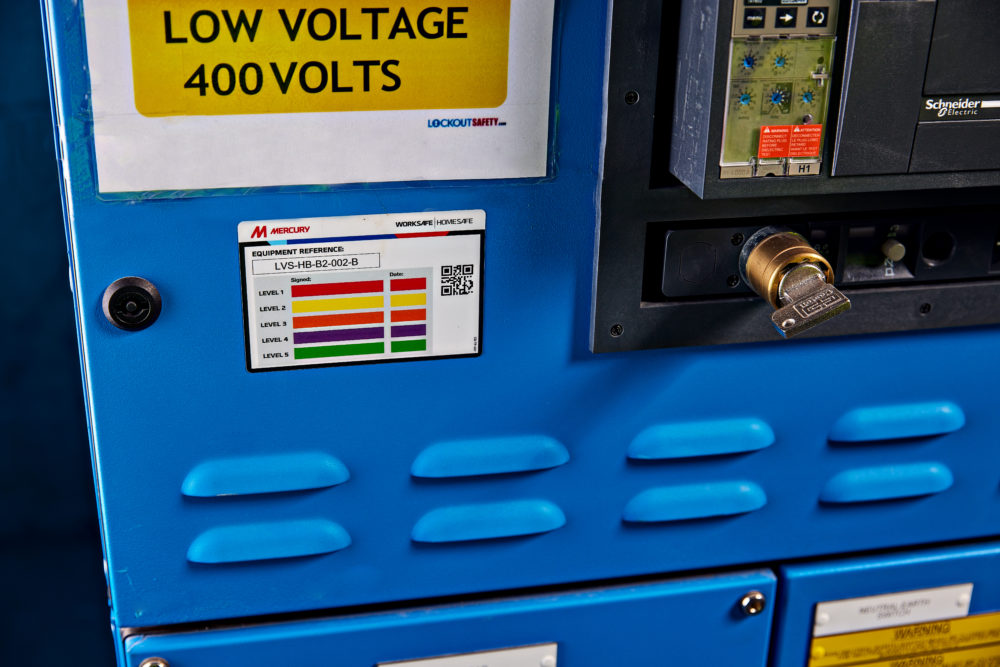
Utilising one central location for all system and asset quality documentation is crucial for delivering projects such as the NCH, efficiently. Overall, this technology contributes to our teams spending more time on site rather than the site office and improves our quality processes ensuring that our clients benefit from the highest standards.
Keith Hore, Group Electrical Programme Manager commented: “BIM360 Field contributes towards improved efficiency on all our projects. It increases communication, improves progress, and can be adapted to work for all projects within the business from healthcare, pharma, data centres, and semi-conductor plants. This construction management software guarantees accountability and maintains responsibilities through all phases of a project. Mercury’s digital innovation department supports this process throughout our operations by generating QR Codes, digitalising project checklists, and ISO9001 compliance Audit Templates”.
DIGITAL EDGE
These digital tools are all initiatives from our ‘Digital Edge’ pillar from Mercury’s Beyond50 strategy. The core goal of this pillar is to deliver a mobile, integrated digital backbone for back office and frontline workers from design through to operations that drives our digital project delivery to the edge. Read more about innovation in Mercury here.